Airbus ZEROe: Emissions-Free Aviation Around the Corner
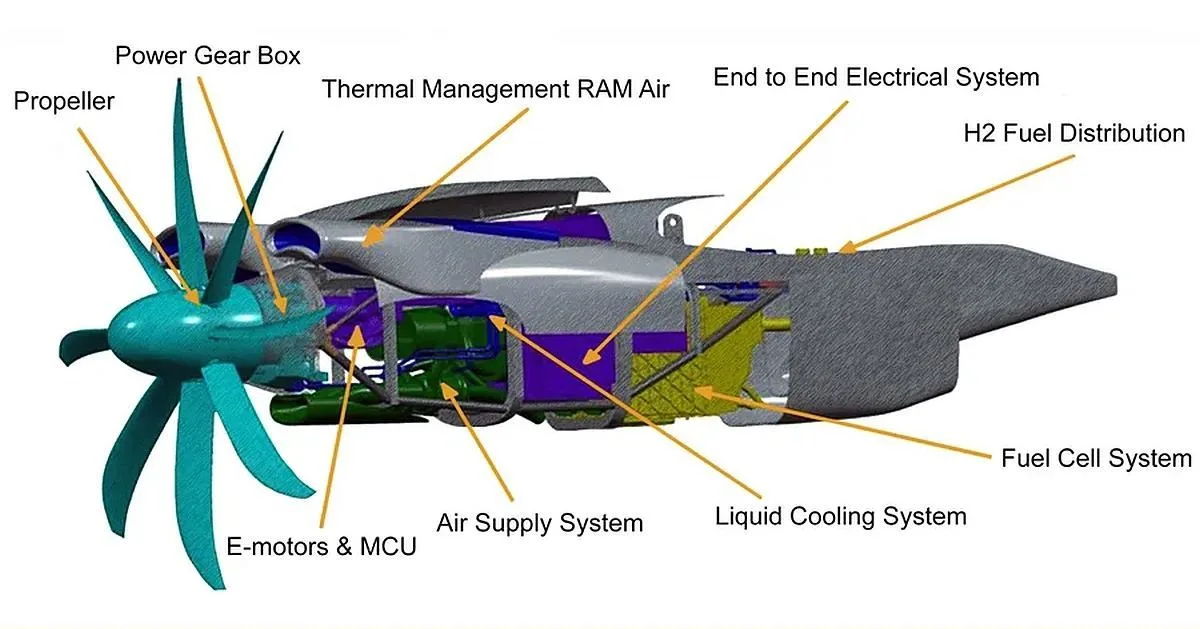
The dream of carbon-neutral air travel is gradually becoming a reality. Airbus’s ZEROe project, first unveiled in 2020, is the company’s bold step toward reducing aviation’s environmental footprint by developing the first hydrogen-powered commercial airliner. The ZEROe project aims to harness the power of hydrogen fuel cells to eliminate carbon emissions in aviation, a sector responsible for about 2-3% of global CO2 emissions. While challenges remain, the project is progressing, with key developments in hydrogen propulsion technology, fuel cell efficiency, and engine design that could shape the future of air travel.
At its core, the ZEROe aircraft represents a radical departure from conventional jet engines. The design, which will initially accommodate 100 passengers, is envisioned to fly up to 1,000 nautical miles (1,852 km)—a range suitable for short-to-medium-distance flights. In place of traditional jet engines powered by kerosene, the aircraft will use hydrogen fuel cells, which generate electricity through a chemical reaction between hydrogen and oxygen, emitting only water vapor as a byproduct.
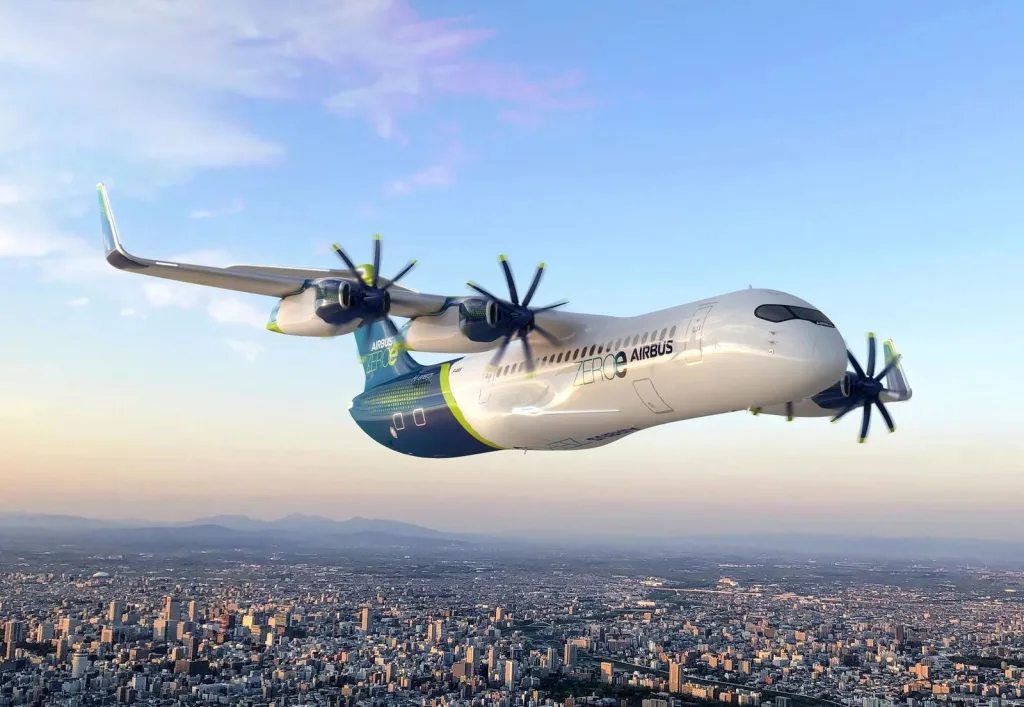
This transition to hydrogen-powered aviation hinges on several technological innovations, with the most notable being the development of fuel cell systems that can provide sufficient energy for flight. Airbus plans to equip the ZEROe aircraft with four hydrogen fuel cells, each capable of producing up to 2 MW of power, giving a total output of 8 MW. These cells will power the electric motors that drive the aircraft’s propellers. Early-stage testing has demonstrated promising results, with a pilot system developed by Airbus and its partners reaching a performance output of 1.2 MW, showing that the technology is progressing toward meeting the requirements for full-scale flight.
In addition to the fuel cell technology, the engine design is equally revolutionary. Airbus is exploring a concept known as the “Open Fan” engine. In this design, the engine’s fan blades are exposed, as opposed to being housed inside a conventional nacelle. This configuration allows for a dramatic increase in the intake of bypass air—up to five times more than traditional engines—resulting in higher efficiency and quieter operation. These benefits are expected not only for hydrogen aircraft but also for kerosene-powered planes, which would see efficiency improvements of 20-30%. Airbus has already tested this Open Fan design in wind tunnels, with the results indicating substantial gains in performance and noise reduction.
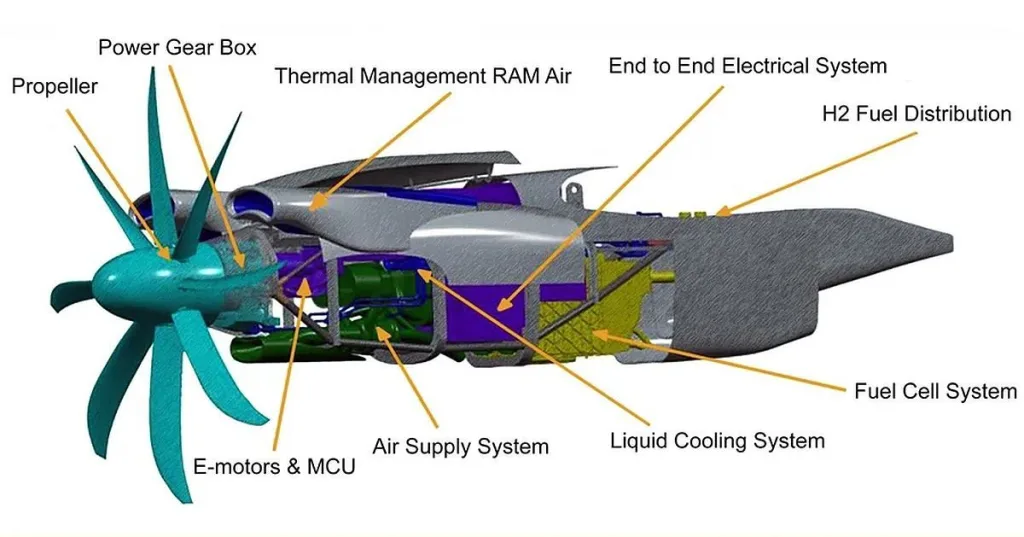
But the development of hydrogen-powered engines is only part of the puzzle. Another key area of focus for Airbus is the use of superconducting electrical systems. These systems promise to enhance the efficiency of the entire aircraft by minimizing energy losses during transmission. By employing superconductors—materials that exhibit zero electrical resistance at extremely low temperatures—Airbus aims to reduce the heat generation typically associated with high-power systems. This technology is still in its experimental phase, but its potential to enhance both fuel cell and motor efficiency could be a game-changer for the aviation industry, particularly for larger hydrogen-powered aircraft that may be developed in the future.
The hydrogen storage system also presents challenges. Hydrogen must be stored at extremely low temperatures—around -253°C—which requires highly efficient insulation and cooling systems. Airbus is investigating innovative approaches to leveraging the cold temperatures of liquid hydrogen not just for storage but also for cooling the aircraft’s electrical systems, helping maintain optimal performance. This approach could ultimately increase the efficiency of the entire propulsion system, benefiting both the aircraft’s power and weight distribution.
However, even with the promise of these advancements, the timeline for realizing the ZEROe aircraft in commercial flight is still uncertain. Originally, Airbus aimed for a 2035 debut. But in a recent statement, Guillaume Faury, Airbus’s CEO, acknowledged that the project’s timeline may need to be adjusted. The slow development of infrastructure for green hydrogen production and the regulatory approval processes for hydrogen-powered aircraft could delay the project further into the late 2030s. Nonetheless, the goal remains clear: to transform aviation into a sustainable industry capable of reducing its impact on climate change.
The Future of Aviation: More Than Just Hydrogen
As Airbus progresses with its hydrogen-powered airliner, the ZEROe project signals a wider shift in the aerospace industry towards greener technologies. The advancements made by Airbus in hydrogen propulsion, fuel cells, and superconductivity could pave the way for a future where emissions-free air travel is not just an ideal but a practical reality. It’s not just about a hydrogen-powered aircraft—it’s about laying the groundwork for a new kind of aviation infrastructure, one that relies on clean energy sources and dramatically reduces the aviation sector’s carbon footprint.
If successful, the ZEROe project could become a model for other industries, influencing the development of sustainable technologies in everything from automobiles to maritime transport. It will take time, significant investment, and continued collaboration between aerospace giants, governments, and energy providers. However, the progress made so far is an encouraging indication that the hydrogen revolution in aviation is not a distant dream but an achievable goal.
The challenges Airbus faces are substantial—regulatory approval, the scale-up of hydrogen infrastructure, and ensuring the commercial viability of the technology. But with its strong technological foundation and ambitious vision, Airbus is positioning itself at the forefront of the clean aviation revolution. The ZEROe aircraft could one day represent the future of air travel, offering a cleaner, quieter, and more sustainable way to take to the skies.
ZEROe Aircraft: Key Technical Features
- Passenger Capacity: 100 passengers
- Range: 1,000 nautical miles (1,852 km)
- Fuel Cells: Four fuel cells (2 MW each), totaling 8 MW power output
- Engine Design: Open Fan Design for increased air intake and efficiency
- Superconducting Systems: Improving energy transmission and reducing heat loss
- Storage and Cooling: Liquid hydrogen storage at -253°C, used for both fuel and system cooling
- Efficiency Improvements: 20-30% increase in efficiency for traditional aircraft
- Timeline: Expected first flight in the late 2030s